Silica Liquid Applications Properties Production
About silica sol
Silica sol is widely used in various fields. Its unique properties are related to its use and its production.
Properties of silica sol
Silica sol has various characteristics. The appearance is often uniform and stable colloidal, and the texture is fine. The particle size of its dispersed phase is very small, mostly between a few nanometers and tens of nanometers. This characteristic makes silica sol have good dispersion and stability, and it is not easy to coalesce and settle for a long time. And because of its colloidal properties, it can be evenly dispersed in many systems, interacting with other substances to improve the overall performance. Its viscosity is moderate, which is convenient for operation and can provide suitable fluidity and adhesion for materials in specific processes. In addition, silica sol has high chemical stability, can resist acid and alkali and other chemicals to a certain extent, and maintain its own characteristics in complex chemical environments.
Application of silica sol
In many aspects of industrial production, silica sol is widely used. In the coating industry, it is often used as an additive to enhance the adhesion, hardness and wear resistance of coatings. Coated on the surface of objects, it can form a dense protective film, improve the protective performance of the coating, and make the coated material durable in harsh environments. In the foundry field, silica sol is a high-quality adhesive. It can effectively bond the molding sand, make the mold have good strength and air permeability, ensure the accuracy and quality of the casting, and reduce casting defects. In the electronics industry, silica sol is also indispensable. It is used in the manufacture of electronic components, such as the packaging of semiconductor devices. It uses its insulation and chemical stability to protect electronic components from external environmental influences and ensure the stable operation of electronic equipment. In addition, in the ceramic, textile and other industries, silica sol can also play a unique role in improving product quality and performance.
Production of silica sol
There are various methods for the production of silica sol. The common one is ion exchange method. First, water glass is used as raw material, and metal ions are removed through ion exchange resin to obtain a pure silica solution. After a series of processes such as concentration and pH adjustment, the silica acid is polymerized to form a silica sol. The silica sol obtained by this method has high purity and narrow particle size distribution. There is also an acid neutralization method, which uses water glass and inorganic acid as raw materials to neutralize under suitable conditions to generate a silica acid gel, and then the silica sol is prepared by decontamination, concentration and other steps. The process of this method is relatively simple and low cost, but the product quality control is slightly more difficult. In addition, there are other production methods such as glue dissolution method, each with its own advantages and disadvantages. The production needs to be reasonably selected according to actual needs and conditions.
Silica sol is widely used in various fields. Its unique properties are related to its use and its production.
Properties of silica sol
Silica sol has various characteristics. The appearance is often uniform and stable colloidal, and the texture is fine. The particle size of its dispersed phase is very small, mostly between a few nanometers and tens of nanometers. This characteristic makes silica sol have good dispersion and stability, and it is not easy to coalesce and settle for a long time. And because of its colloidal properties, it can be evenly dispersed in many systems, interacting with other substances to improve the overall performance. Its viscosity is moderate, which is convenient for operation and can provide suitable fluidity and adhesion for materials in specific processes. In addition, silica sol has high chemical stability, can resist acid and alkali and other chemicals to a certain extent, and maintain its own characteristics in complex chemical environments.
Application of silica sol
In many aspects of industrial production, silica sol is widely used. In the coating industry, it is often used as an additive to enhance the adhesion, hardness and wear resistance of coatings. Coated on the surface of objects, it can form a dense protective film, improve the protective performance of the coating, and make the coated material durable in harsh environments. In the foundry field, silica sol is a high-quality adhesive. It can effectively bond the molding sand, make the mold have good strength and air permeability, ensure the accuracy and quality of the casting, and reduce casting defects. In the electronics industry, silica sol is also indispensable. It is used in the manufacture of electronic components, such as the packaging of semiconductor devices. It uses its insulation and chemical stability to protect electronic components from external environmental influences and ensure the stable operation of electronic equipment. In addition, in the ceramic, textile and other industries, silica sol can also play a unique role in improving product quality and performance.
Production of silica sol
There are various methods for the production of silica sol. The common one is ion exchange method. First, water glass is used as raw material, and metal ions are removed through ion exchange resin to obtain a pure silica solution. After a series of processes such as concentration and pH adjustment, the silica acid is polymerized to form a silica sol. The silica sol obtained by this method has high purity and narrow particle size distribution. There is also an acid neutralization method, which uses water glass and inorganic acid as raw materials to neutralize under suitable conditions to generate a silica acid gel, and then the silica sol is prepared by decontamination, concentration and other steps. The process of this method is relatively simple and low cost, but the product quality control is slightly more difficult. In addition, there are other production methods such as glue dissolution method, each with its own advantages and disadvantages. The production needs to be reasonably selected according to actual needs and conditions.
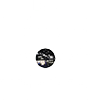
Scan to WhatsApp